Ontdek verborgen potentieel in uw wasserij
De IT-oplossing waarmee de productiviteit 4 tot 35 procent toeneemt
Van inspiratie naar rendement
Als teamwork en slimme automatisering samenkomen, gebeurt er iets moois. Laundry Dashboard brengt unieke informatie in de wasserij. Dat leidt zelfs in de beste wasserij tot inspirerende verbeteringen.
1. Ga de uitdaging aan
Hoe goed uw productiviteit ook is, het kan nóg beter. Ga de uitdaging aan.
2. Stuur op data
Monitor uw wasserij als nooit tevoren en ontdek wat er gebeurt.
3. Verbeter samen
Professionele wasserijen realiseren 4-35% performancewinst.
Doe ook een test!
Bent u benieuwd hoe Laundry Dashboard werkt in de praktijk van úw wasserij? Overtuig uzelf dan met behulp van onze unieke testopstelling. De testopstelling kan eenvoudig door uzelf worden geïnstalleerd.
- Binnen drie weken leverbaar
- Plug & play
- Gratis training
- Direct resultaat
- Drie maanden geen licentiekosten
- Niet goed, geld terug
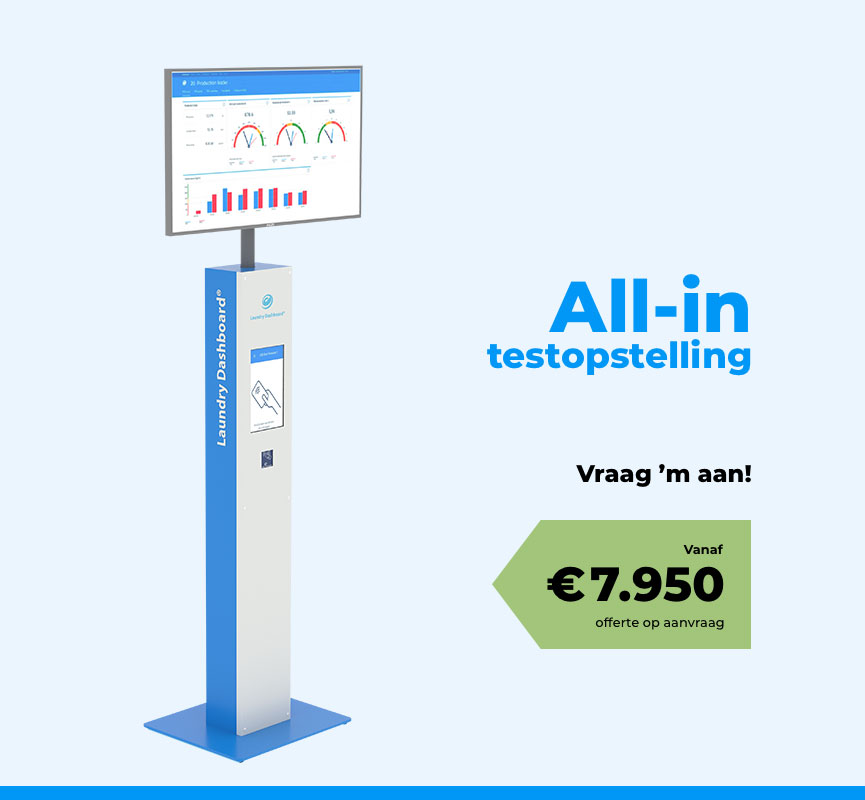